I'm building another guitar! Just a reminder really, but it is such fun to see these things take shape. The electric guitar is basically a stick, bolted to a board with some strings tied on to it. Watch the movie It Might Get Loud to see Jack White make a guitar out of a front porch, a coke bottle, a string and a couple of nails. Anyway, the acoustic guitar is self-propelled in a manner of speaking. All of its volume is produced by the woods/other materials, a vibrating mass (the strings) and physics. Consequently, there is a lot more going on with the construction. Our first steps include sanding the wood for the top to the proper thickness. This varies according to the type of wood, type of guitar and so on. Check my previous posts to see this piece of wood as it came to me.
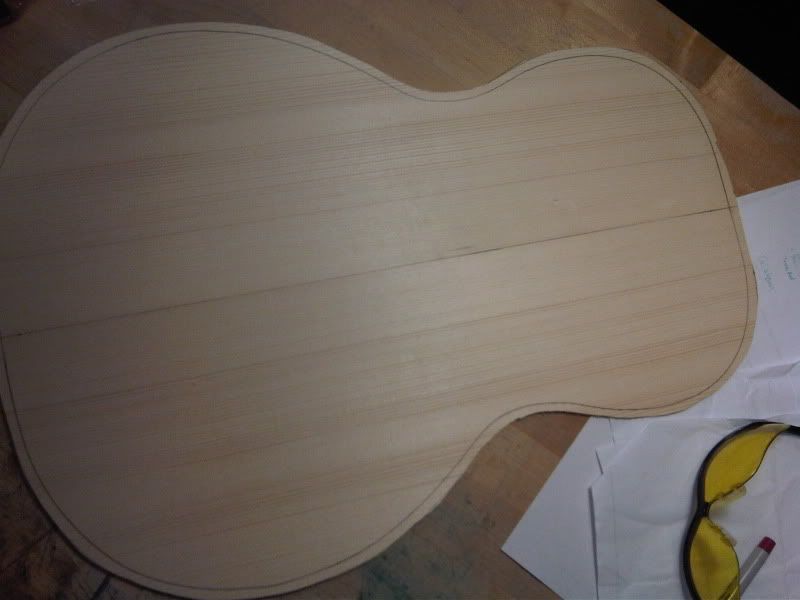
Next, we cut out the shape on the band saw. I'm building a Martin-style "Single O" guitar. It will look sorta like this.
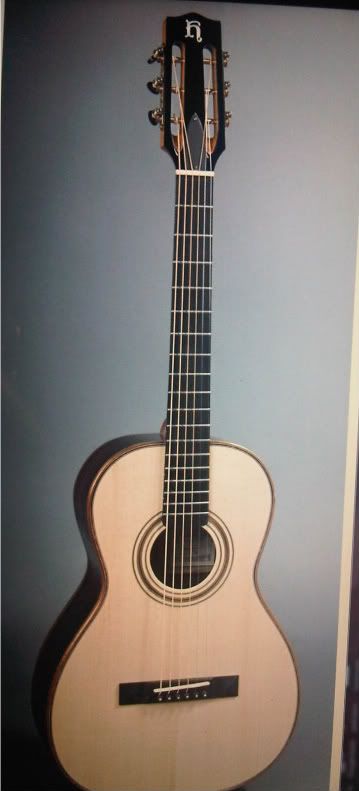
The guitar in this image was built by Charles Hoffman, a well known Minneapolis luthier. The Single O is a wee guitar that often has a beautifully sweet voice and they are especially well-suited for solo guitar work.
After some head scratching, we route a channel and install the rosette. Besides adding some aesthetic spice to the top, the rosette is functional in a small, but important way. I kept mine understated so as not to distract from any of the many subtle charms this guitar will possess. It's Abalone wrapped in two very thin purfling strips. Getting this installed was a forehead wrinkling endeavor, to be sure.
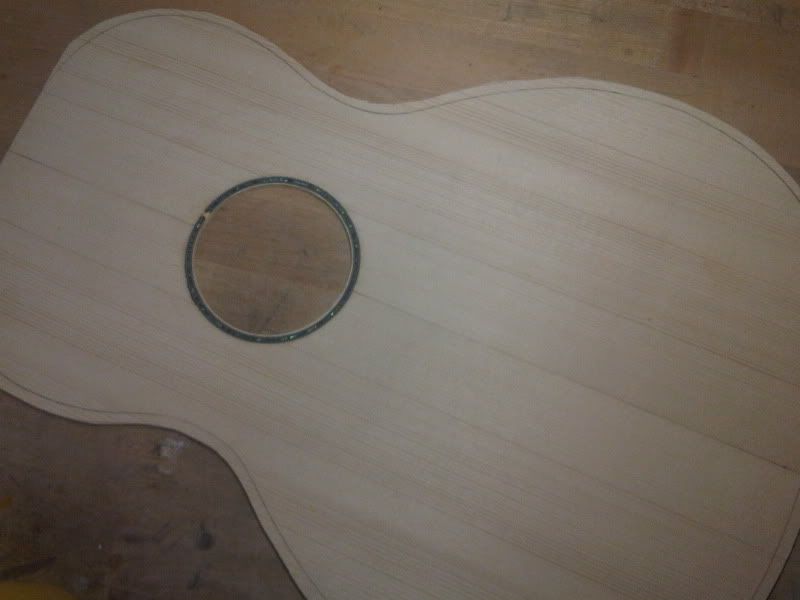
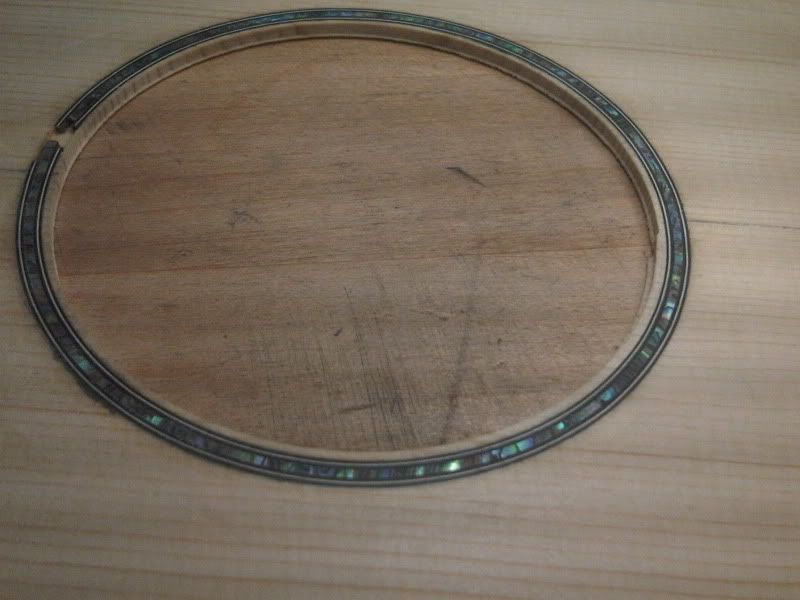
When a guitar is all strung up to the proper pitch, there is a huge amount of tension created by the strings. There are several factors involved in the exact figure but it can range well over a hundred pounds. An acoustic guitars top, back and sides thicknesses are way under 1/8 of an inch and so something has to bear the brunt of all of the string tension. Enter, the brace. Most are carved from spruce because it has an exceptional strength to weight ratio. The big daddy of all the braces is the X brace. If you squint, you can see pencil lines marking the layout for all of the other braces.
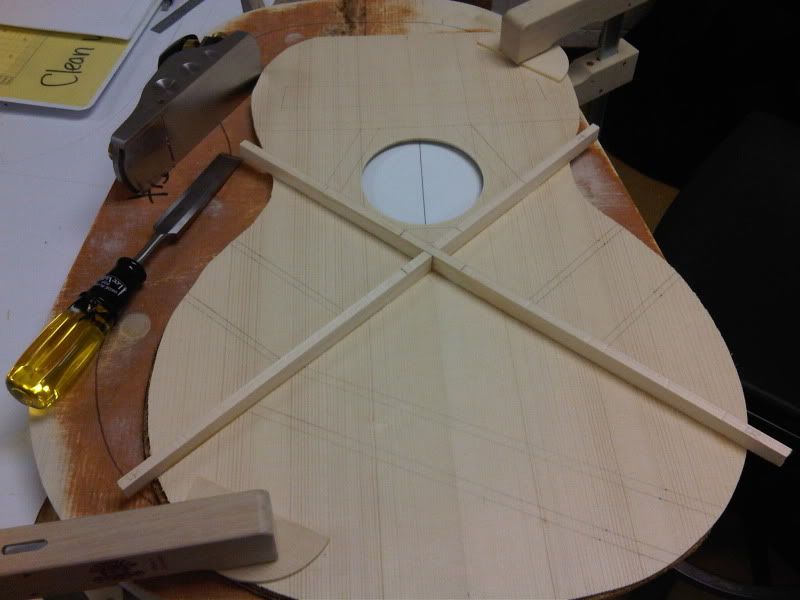
X brace. Aptly named, no? Once that chunk is glued on, you taper and scallop it in order to maximize the strength where it is needed and reduce the stiffness where it is not. Most guitar builders, from the big guys at Martin and Gibson all the way down to the high-end boutique producers have their own way of doing this. I am utilizing the Martin style. All the carving is done using a block plane, a very sharp chisel and a wee finger plane.
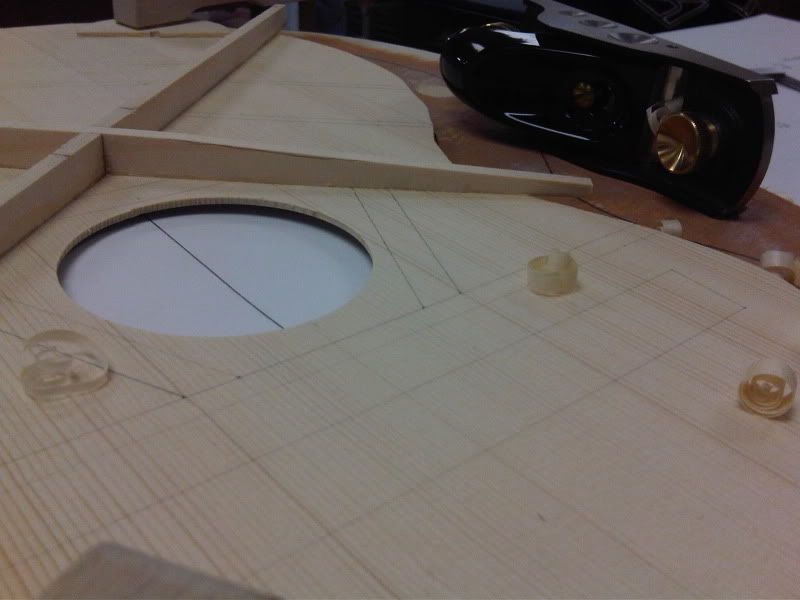
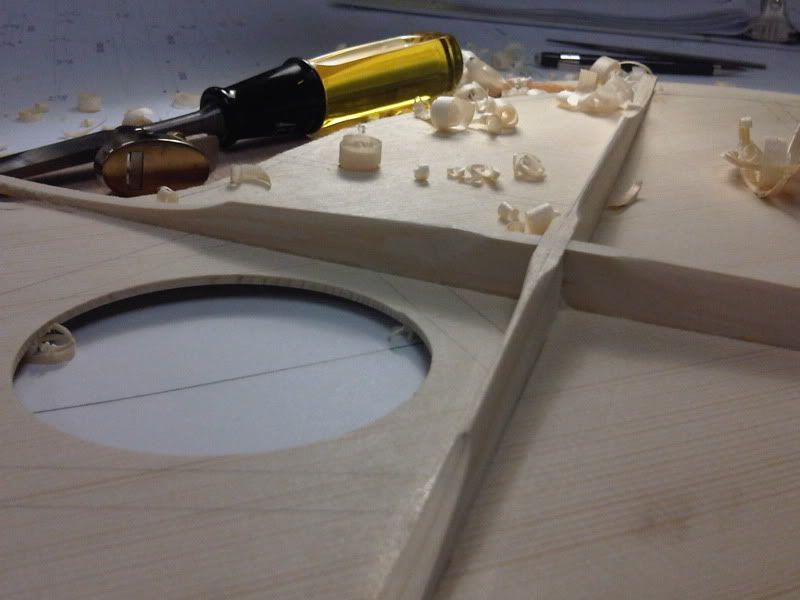
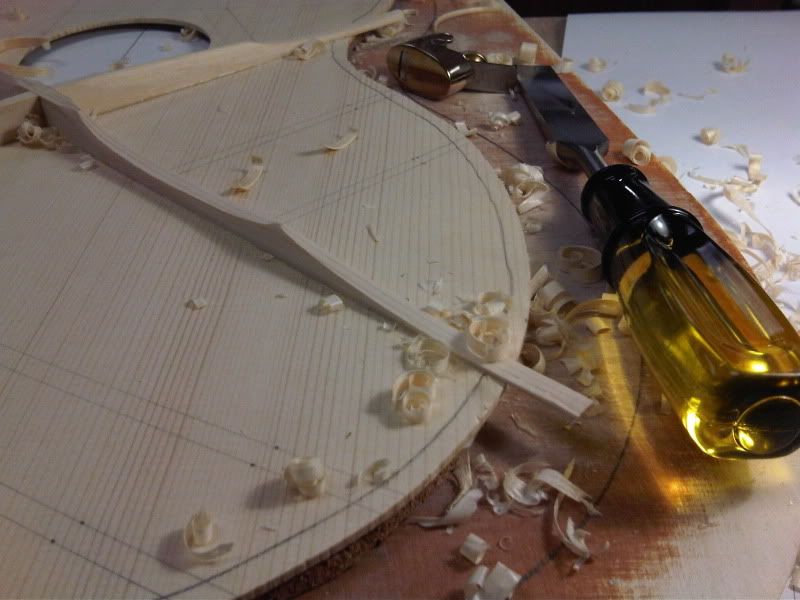
All of the brace carving you've seen here was whipped out today. There are a half-dozen more of these braces that will get carved, then glued on in the next couple of days. Once that is out of the way, we will glue the wood for the back of the guitar together and begin the process of bending the wood for the sides. Sweet! Stay tuned.
One final word before I hit the sack. Please take a moment to do something for our fellows in Japan. Send money, send prayers or send up gratitude for all that we have here in the USA. Bonsoir...